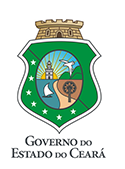
The housing shortage situation has forced India to increase the bricks and cement production. The procedure of conventional brick production involves topsoil removal from fertile land at the end of every agricultural season. The consequences of the activities are releasing a large amount of GHG emissions, degrading the soil, and also threatening the farmers from losing their fertile land.
These challenging issues are being addressed by a new approach for brick production, which uses fly ash, a by-product from thermal power plants, instead of topsoil from a fertile productive land.
The solution aims at creating a low carbon economy that can contribute in alleviating poverty by increasing job availability and reducing environmental impacts at the same time.
The inspiring green business initiative was spearheaded by Development Alternatives (DA), a research based Non-Governmental Organization (NGO) in 2014. Fly ash brick offers a simple low-tech solution to make more sustainable and eco-friendly bricks. The technology has been developed by TARA, a social enterprise that is part of a wider NGO group – Development Alternatives. Compared to standard brick production, fly ash bricks provide several advantages, as:
This simple and low-tech technology introduced by TARA is basically a press machine to produce fly ash bricks. Generally, the machine consists of a raw material mixing chamber, mixture conveyor, moulds for the brick, a hydraulic system, and an electronic control panel. The operation of the fly ash brick machine is simple. The first step is to mix all of the materials, consisting of sixty-two per cent of fly ash, twenty-five per cent of quarry dust, eight per cent of hydrated lime, and five per cent of gypsum. All materials are mixed together with water to achieve the desired mixture consistency. After mixing, the conveyor transports the mixture into the moulds to have it pressed by the machine and make it compact. The last step in the process is to let them dry under the sun and water-cure for seven to fourteen days.
With this machine, the workers could produce the bricks faster and easier. One machine can produce up to 1450 fly ash bricks per hour depending on the type of machine. In addition to environmental benefits, various social benefits are also associated with the commissioning of new fly ash units, as the establishment of new units creates new employment opportunities especially for women.
The use of fly ash brick offers an opportunity for a productive use of waste, while preventing emissions and creating jobs for the local community. DA has been working in several states of the country towards the development of fly-ash brick industry, including Bihar, Odisha, Madhya Pradesh, Maharashtra, Orissa, Delhi, Jharkhand, Chhattisgarh and Haryana. According to DA’s recent report, the state of Bihar produces approximately eighteen billion traditional bricks per year using approximately six thousand kilns produced from Fixed Chimney Kilns (FCKs), which are resource- and energy-intensive, as the predominant technology in the state.